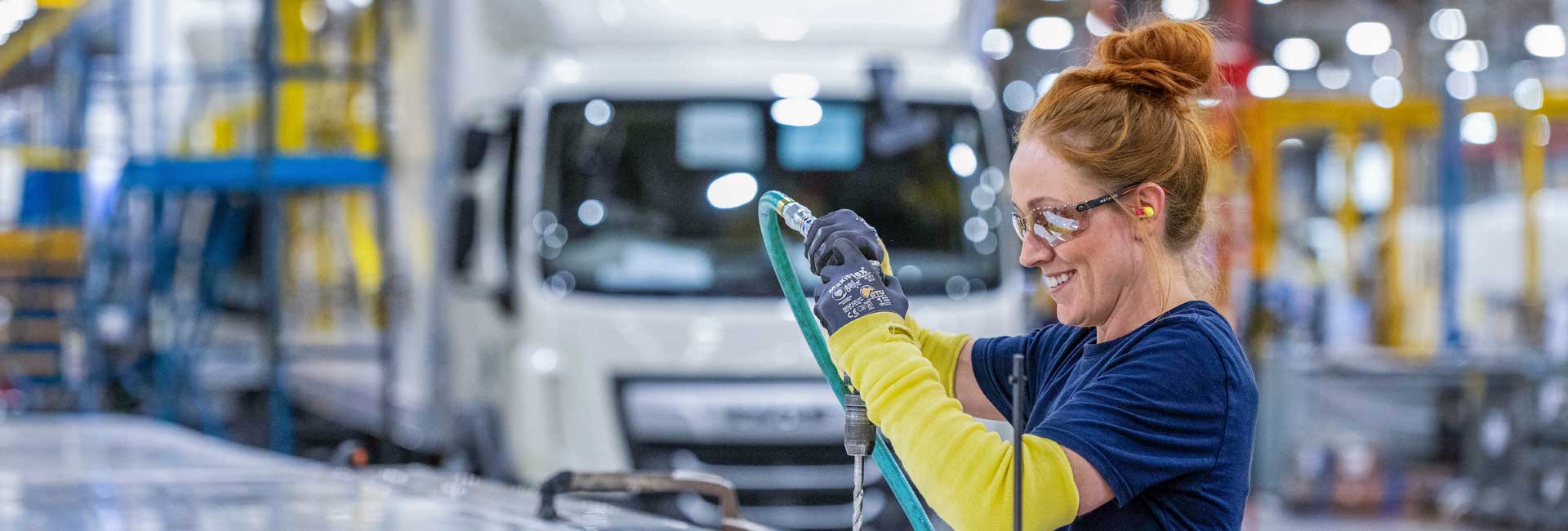
Sustainable production facilities
DAF is pursuing multiple initiatives to meet its 2030 ambition of a 45% reduction in Scope 1 and 2 CO2 emissions (compared the 2018 baseline year). This ambition is supported by a CO2 reduction roadmap supplemented with clear action plans covering all the company’s production sites.
Progress realized in all plants
In 2024, DAF Eindhoven, Westerlo and Leyland combined, implemented 21 initiatives to improve energy efficiency or to reduce gas usage, which collectively reduced CO2 emissions by over 3,000 tonnes. Key projects include the installation of heat pumps, the expansion of LED lighting in buildings, and installing additional solar panels.
Upgade chassis paint booth
An example of CO2 and energy reduction being realized is the upgrade to the Eindhoven chassis paint booth in the summer of 2024. Redesign of the air circulation system makes it possible to better manage temperature and airflow, resulting in a more comfortable working environment and reduced energy needs. Integration of a heat recovery system allows us to reuse warm air from the cooling tunnel, further decreasing the need to heat incoming air. This saves approximately 700 MWh of heat annually, cutting gas consumption by about 81,500 m³.
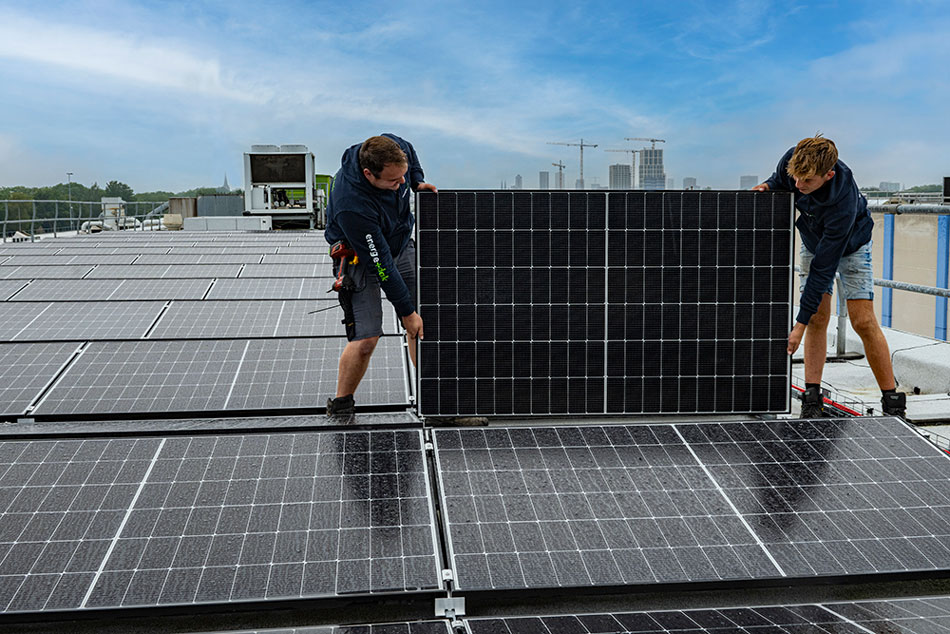
Solar panel installation plan
The project to enhance the sustainability of our central warehouse where truck components for production are stored, started in 2021 with the insulation of the roof. As a next step, the existing air handling units were replaced with a low-temperature system with waste heat recovery that utilizes less energy and operates more efficiently. In 2024, solar panels were installed on the roof as part of an extensive solar panel installation plan for Eindhoven and Westerlo.
In 2025, in the central warehouse, a system to feed the air handling units with waste heat from the Engine Test Center will be integrated. This will maximize energy efficiency and further reduce carbon emissions. We have started to upgrade the walls and roofs of the axle plant in Westerlo, Belgium. New insulation guarantees a comfortable working temperature for the employees, while reducing energy to heat the buildings. The expected saving is 800 MWh of natural gas per year.
Full suite of innovations in Westerlo
In Westerlo, in the axle paint booth, robots that had reached the end of their lifespan, were replaced with two new high-pressure paint robots. This has improved paint quality and has reduced overspray by approximately 50%. A new blow-off system ensures that axles are thoroughly dry before they enter the paint booth, eliminating the need for extra heating or cooling. A new dry filtration system resulted in enhanced air quality and reduced noise as well as chemical waste from the painting process (20 tons per year).
In 2024, high priority was given to solving leakages in the compressed air system. Mobile air leakage devices have been purchased for our facilities in Eindhoven and Westerlo, and in Leyland an Air Leak Survey was conducted by an external contractor. Significant progress was made in repairing air leaks for reduced noise levels in the factories and enhanced energy efficiency across our operations. DAF Westerlo alone saved over 6,000 kg CO2 emissions by structurally solving air leakages.
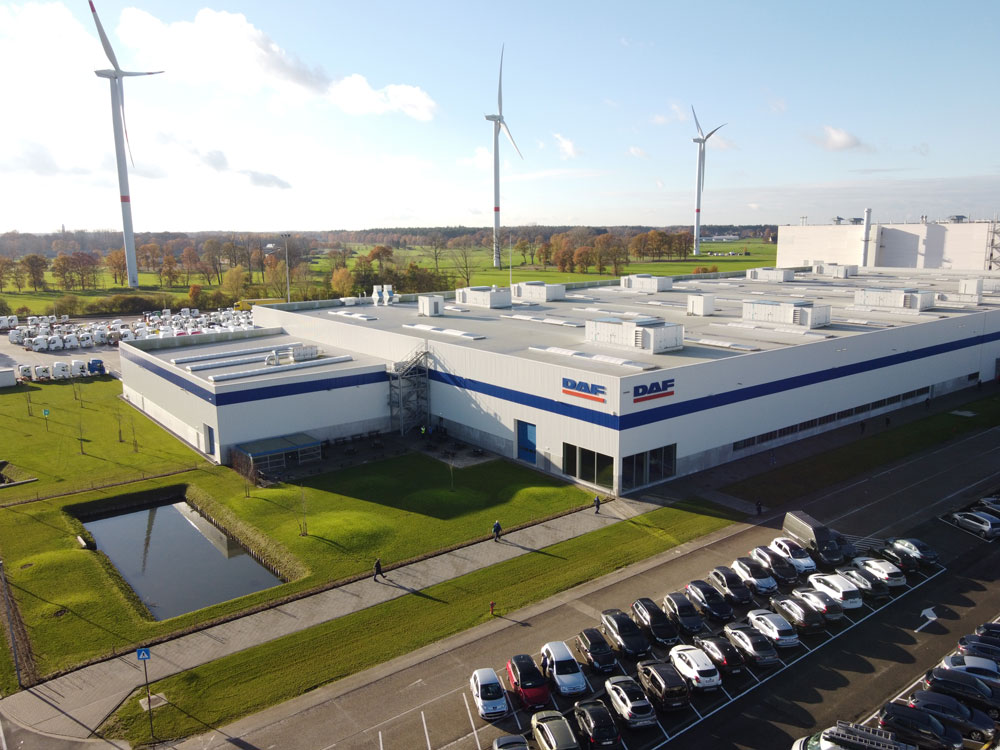
ISO 14001
For over 25 years we deploy an environment management system to monitor our environmental impact. As one of the first large companies in Europe, DAF has been ISO 14001 certified since 1998. This ISO 14001 certification underlines our effort to addressing environmental impacts stemming from our operations, such as air pollution, water usage, waste treatment, resource use, climate change mitigation and adaptation. Internal audits are routinely conducted to ensure the effectiveness of the policies and procedures we have implemented at our production facilities, the engineering test track, and the European parts distribution centers, used-truck centers and sales subsidiaries. Each DAF department is responsible for seeking continuous improvements towards mitigating negative environmental impacts. We expect that all European DAF dealers have an ISO 14001 certificate or are in the process of obtaining this.
Energy dashboard
We have introduced an energy dashboard that tracks energy consumption in all our manufacturing facilities. This tool allows engineers to analyze energy usage patterns and collaborate with production teams to identify areas for improvement. Where possible, machines are shut down when they are not in use and settings are adjusted to optimize energy efficiency.
Climate campaign
At the Belgium manufacturing facility, a Climate Campaign promotes employees to identify energy waste and report it to supervisors and the environmental team, fostering a proactive approach to sustainability. Additionally, a competition invites team members to propose energy-saving solutions, with rewards for the best ideas. Together, we are not just reducing our environmental footprint; we are building a culture of sustainability at DAF.
PACCAR Distribution Centers (PDCs) focus on reducing emissions
In November 2024, PACCAR Parts opened an industry leading Parts Distribution Center (PDC) in the city of Massbach, Bavaria, Germany. It further strengthens the industry-leading parts supply for DAF dealers and customers across Germany, Switzerland, and the Eastern part of France. The new PDC also reaches high standards in sustainability.
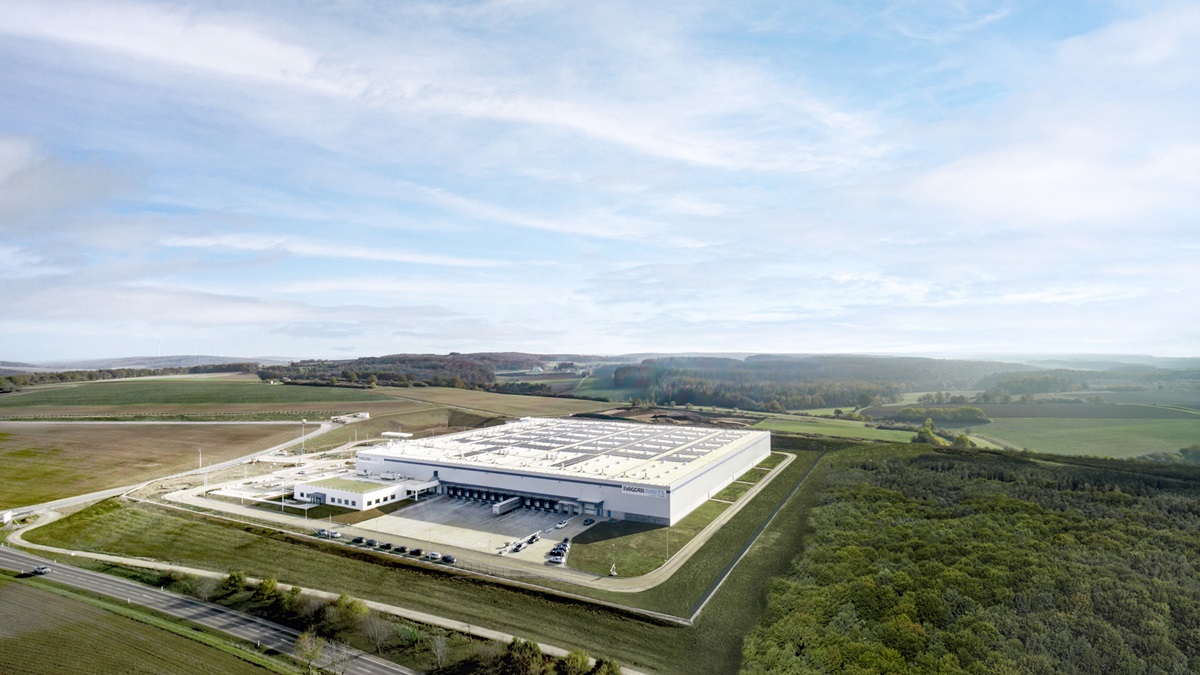
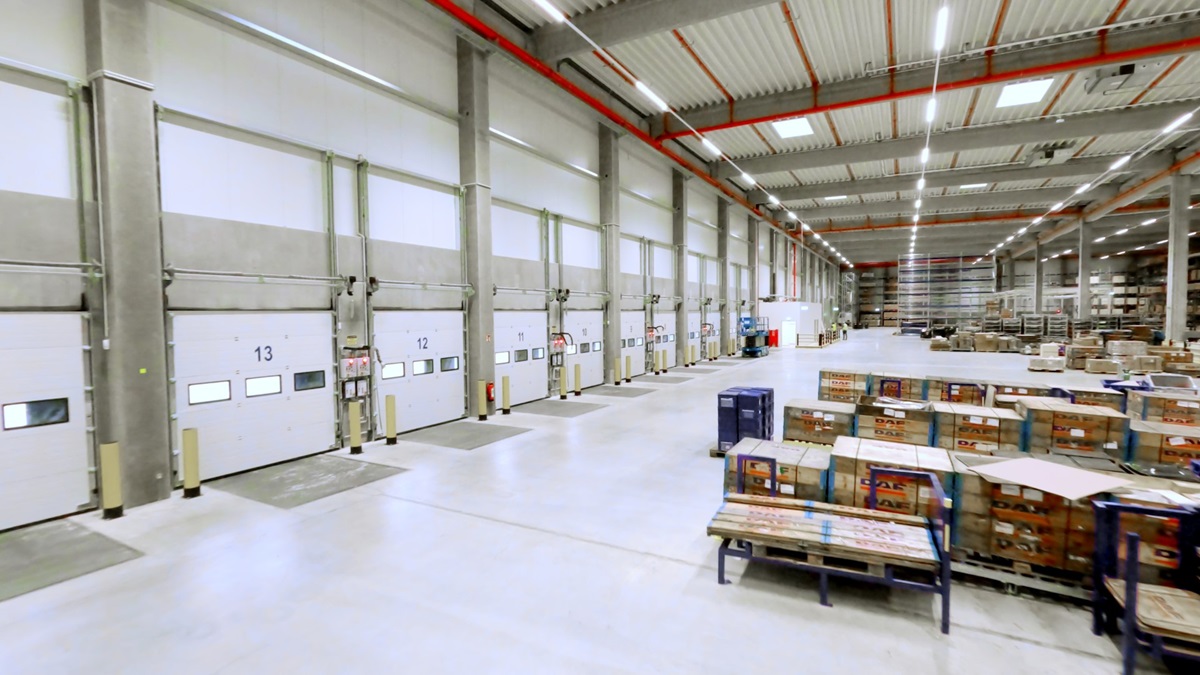
The Massbach PACCAR Parts Distribution Center spans 25,000 m2 and has the capacity to hold over 80,000 unique parts. This facility is net-zero; site electricity needs are generated by 4,000 lightweight solar panels, with any surplus energy directed to a battery storage system which can be used to charge electric trucks visiting the site. The office building has a green vegetation roof system to provide insulation and an eco system for nature whilst energy efficient heat pumps help maintain a constant temperature inside of the PDC all year round.
Other PACCAR Parts Distribution Centers made steps to lower emissions. Over the last two years, gas usage reduced by 40% in the PDC in Eindhoven, the Netherlands. This was achieved by lowering the temperature within the PDC by 1 degree, following a successful test where employees were still happy with the lower temperature. Dock shelters were installed to reduce the draught, opening and closure of sluice gates are now aligned to keep the cold outside, and LED Lighting was implemented, saving 303 MWh annually. In addition, the PDC’s technical room has been prepared for solar panel installations.
Related information
Go back to...